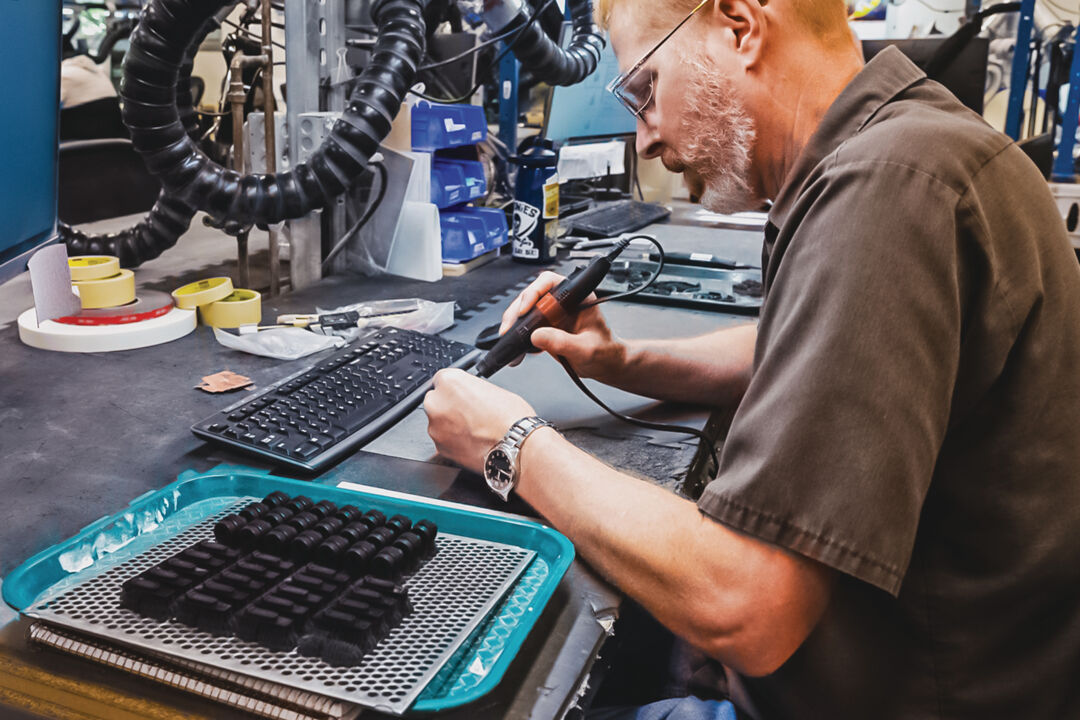
Automation has streamlined many of the post-processing operations common to 3D printing, yet the need for skilled labor isn’t going away anytime soon.
My dad was a commercial artist. He frequently mentioned the service bureau that converted his hand-drawn illustrations into brochures, catalogs and signage. One Saturday, he needed to drop off a hot job, so I accompanied him to a massive glass-fronted building in downtown Minneapolis. To a small boy, it was a magical place, with seemingly endless lines of hulking Linotype machines and offset printing presses, the air redolent with the smell of ink, solvent and paper.
Neither my father nor I knew it then, but that day also marked the beginning of the end of an era. Not only was the printing industry about to become both digital and largely on-demand, but the term “service bureau” would soon take on an entirely different meaning.
Feel the Magic
Anyone visiting a service bureau today will encounter equally magical machines, but ones that print vertically as well as horizontally. And thanks to the one-stop shop business model shared by several of the firms you’re about to hear from, services often extend well beyond 3D printing. CNC turning and milling, plastic injection molding, sheet metal fabrication—these are but a few of the processes listed on a typical “manufacturing-on-demand” service provider’s website.
Each of these companies also has a broad, sometimes global, network composed of wholly owned manufacturing facilities, a network of independent partners who provide some or all of these services—or a combination of each.
It’s a glorious, choice-filled time for anyone purchasing manufactured products. The challenge then becomes: How do I design parts that can be made using any of a dozen or so distinct 3D-printing technologies? Compounding this confusion is the potential for hundreds of different polymers and metals, the need for secondary post processing and considerations about the often inevitable transition to “traditional” manufacturing processes as quantities rise.
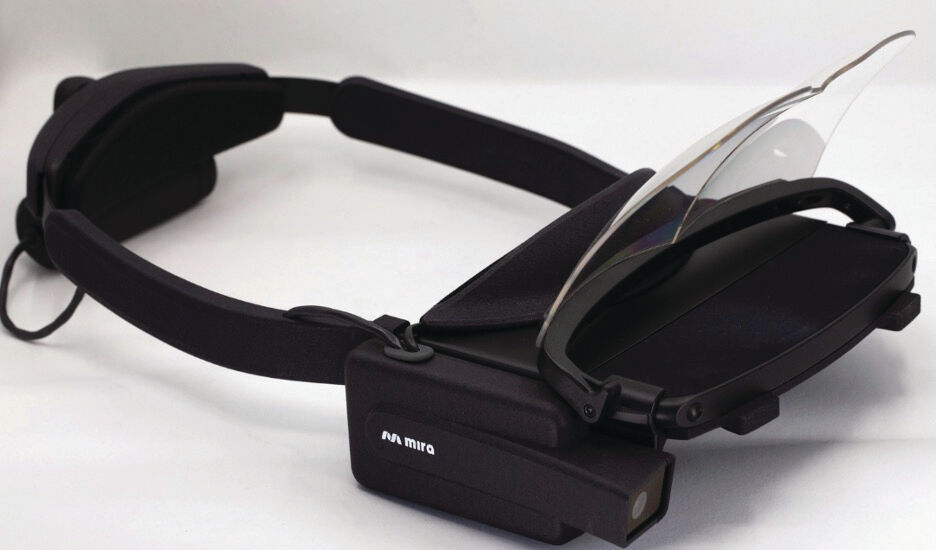
Fictiv’s multi-jet fused, 3D-printed parts assembly for Mira Labs, an AR company.
We’re not going to answer that question here. Everything a designer or procurement professional should know is readily available on website resource pages of 3D-printing providers. Add the hundreds of knowledgeable support personnel working at these companies—all just a chat, email or phone call away—and there’s simply no reason to upload a “bad” design. Right? Maybe not.
Let’s Chat
Manufacturing is a hugely complex science, and even experts with years of experience are often left scratching their head over design choices and determining the most efficient, cost-effective path forward. Additive manufacturing (AM) in particular can be challenging due to its relative freedoms and potential, never mind its continuously evolving capabilities.
“One of the most common design mistakes we see customers make is overlooking the environment in which the 3D-printed parts will be used,” says Riley Hall, senior director of additive at San Francisco-based Fictiv Inc. “For example, we had a customer that wanted a painted finish on their parts. But since the parts were going to be installed in an environment where acetone was prone to splatter, paint was a poor choice. In the end, we had to mask one area of the part prior to painting in order to avoid any potential damage to the finish.”
Making certain that the material and its painting, coating or plating is suitable for the end-use environment is good advice no matter how the parts are manufactured. To address these concerns, Fictiv has developed its Materials.AI artificial intelligence tool, which leverages a generative pre-trained transformer (GPT) language model developed by another San Francisco company, OpenAI.
AI-powered tools for material selection and design-for-manufacturability (DFM) feedback can be incredibly helpful to avoid many common 3D-printing design mistakes, according to Hall, but it’s also helpful to have a team of experts you can talk to about more complex projects and design decisions.
Similarly, it’s critical to select the best 3D-printing process for your application. Hall explains that choosing the wrong one can lead to parts with weak structural integrity, inflated costs, subpar material performance, poor surface finish or a lack of scalability.
One example of this comes from a customer making fuel tanks for drones that had previously used selective laser sintering (SLS) for its prototypes. “Unfortunately, SLS materials are quite porous, so eventually the parts would leak,” Hall says. “In this case, we applied a special epoxy to the parts on the inside, which also added necessary strength. Decisions like these can be nuanced, so it’s quite helpful to have a manufacturing partner you trust to help guide you through the various design considerations.”
Another common design mistake centers around 3D printing’s scalability and knowing when it’s the right time to consider alternatives such as urethane casting or plastic injection molding. 3D printing end-use parts is a good choice when you want to get working products in the hands of customers, Hall notes, especially if they are still relatively early in the product lifecycle and may still be making design changes.
“This is why multi-jet fusion was an ideal choice for our customer Mira Labs, who wanted to do a small, cost-effective run of products for their augmented-reality headset. But at a certain point, once the design is stable and you’re looking toward scale, urethane casting or injection molding can be a better choice.”
Time to Print
Scalability is a key determining factor, agrees Chloe Vollaro, a field application engineer at Minnesota-based Protolabs Inc.’s Morrisville, N.C., facility. “The number one problem is that part quantities are way too high for 3D printing, followed closely by their being too large or too bulky for the technology the customer has selected,” she asserts.
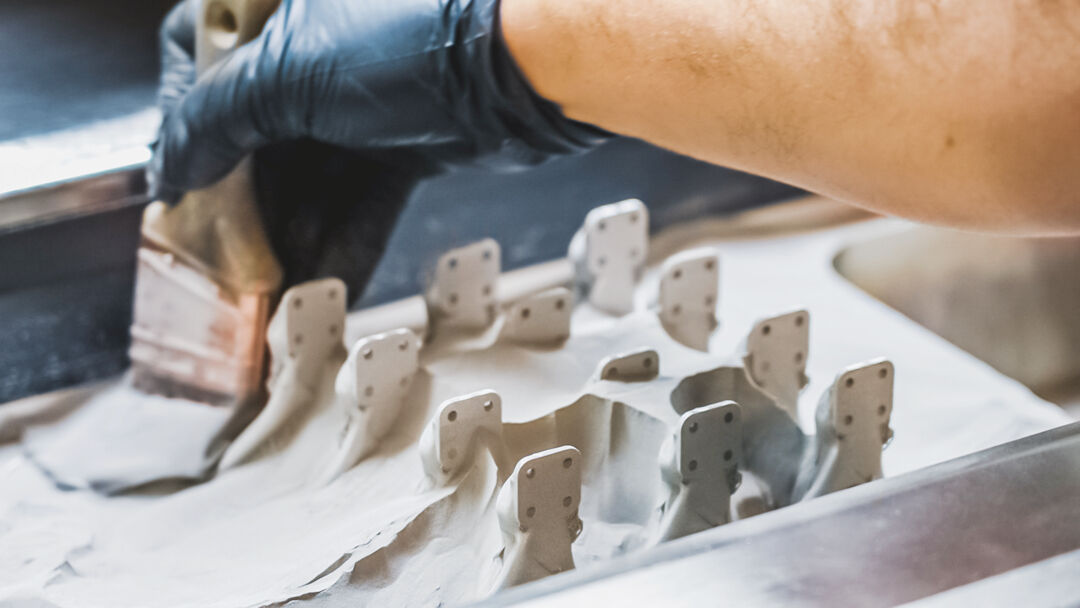
Depowdering is a necessary post-processing step with any powder bed printing technology.
The first of these—high production volumes—is easily addressed by moving the part to plastic-injection molding or, for metal parts, a combination of machining, casting or, perhaps, metal-injection molding (MIM). Yet quantities once considered too high volume for AM are now commonplace. “It depends on the printing technology,” Vollaro says. “For instance, direct-metal-laser sintering (DMLS) is one of the slowest AM processes, but for one customer, we use it to make thousands of tiny rectangular parts that we just clip off the build plate afterward, then they’re done. And with selective-laser sintering or multi-jet fusion, there’s no need for supports so you can fill the entire build chamber. Here, it’s no big deal to print hundreds of small parts.”
The build chamber in each of these applications is relatively small, somewhere between a toaster oven and a carry-on suitcase. Large-format, fused-deposition-model (FDM) printers bypass this limitation, with some able to build parts measuring one meter or more in each direction, albeit with lower part accuracy than the technologies just described.
Regardless, designers should recognize a universal truth about 3D printing: The more material added, the longer the build and the higher the part cost. This equation is the exact opposite of machining, where every cubic inch of material removed adds to the cycle time and therefore the piece price. Of course, this doesn’t account for the material cost itself; polyetheretherketone (PEEK) and other pricey polymers or metals such as titanium and Inconel, can easily break that rule of thumb.
“Finished part cost is primarily driven by print time with AM, and big, chunky parts just take a long time to make,” Vollaro says. “They’re also more susceptible to warpage, stress cracking and other defects, which is why I encourage customers to work with us on their part designs. For instance, many do not realize the advantages of incorporating meshes and lattice structures into their builds. Using these reduces both build time and material consumption, both of which help with part cost, but they also make the parts lighter.”
Redesign to Win
A willingness and ability to redesign parts is often critical with AM, but sometimes it’s not enough. “Years ago, I did a feasibility study for a tractor/trailer manufacturer that brought us a hydraulic component. It was comprised of a series of tubes attached to a pair of welded plates, one on each end. The customer was convinced they could 3D print them more cheaply than using their legacy process, but even with extensive design optimization, there was no way to hit their target price. Some parts just aren’t a good fit for AM.”
That’s according to Greg Paulsen, director of applications engineering and marketing for Xometry Inc., based in North Bethesda, Md. Countless others have heard this message loud and clear. “I’ve seen all sorts of parts where additive is a robust solution, but you do need to take a step back from what you’re currently doing and rethink the whole thing,” Paulsen adds.
This critical step of “rethinking the whole thing” includes when the product enters production. Too many part designers focus on prototyping, Paulsen explains, only to discover that the design freedoms made possible with AM don’t translate to higher-volume processes such as injection molding or machining.
“We had a medical customer that developed an assistive device for people with Parkinson’s disease and similar motor control difficulties,” he notes. “They’d prototyped and tested the product, and were far down the road to FDA certification before they began evaluating how to bring it to market. However, it had several undercuts and inconsistent wall thicknesses that made it almost impossible to injection mold. But with our help, they ended up completely redesigning the part and actually had to split it into two components to make it work,” Paulsen says.
Understanding any manufacturing technology’s accuracy capabilities is similarly important. Paulsen notes that many companies own desktop FDM printers and use them for prototyping, only to find that industrial AM equipment delivers much higher quality. This can be a double-edged sword.
“We had a customer comment that the parts we’d printed with SLS didn’t fit into the assembly like the ones they’d made in-house. ‘Everything is loose,’ they told me,” Paulsen continues. “As it turns out, our parts were much closer to nominal than their personal desktop machine, so there was a lot more play between them. Here again, they ended up redesigning after the fact, and this is yet another instance where working closely with your manufacturing partner can save you a great deal of grief and expense down the road.”
Paulsen closes with the following advice: Learn the DFM rules for every process you intend to use. “Just on the additive side, we offer nine 3D-printing technologies that we’ll auto-quote, and have access to even more outside our menu. Each has its own design rules, and from a DFM perspective, all are significantly different and, in many ways, more flexible than those used with traditional manufacturing processes, which we also offer. It’s therefore imperative that you ask questions and set expectations early on.”
Following the North Star
Stratasys Direct Manufacturing, of Eden Prairie, Minn., doesn’t offer machining or sheet metal fabrication services. This allows the company to focus on its core competency: polymer printing.
“We recently divested out of conventional technologies as well as urethane casting and even metal printing,” notes Gurvinder Kahlon, vice president and general manager. “Our intent was to align around Stratasys’ North Star, which has long been FDM printing but now includes newer technologies such as high-speed, selective-absorption fusion and programmable photopolymerization, a form of digital light processing, or DLP.”
Kahlon points out that, for customers looking to transition to higher-volume processes such as plastic injection molding, Stratasys Direct has a network of partners able to support this need. He also says, as evidenced by the sheer growth and number of providers in this space, it’s a straightforward exercise to invest in a handful of 3D printers and open a service bureau; what’s less clear is solving AM’s more challenging problems.
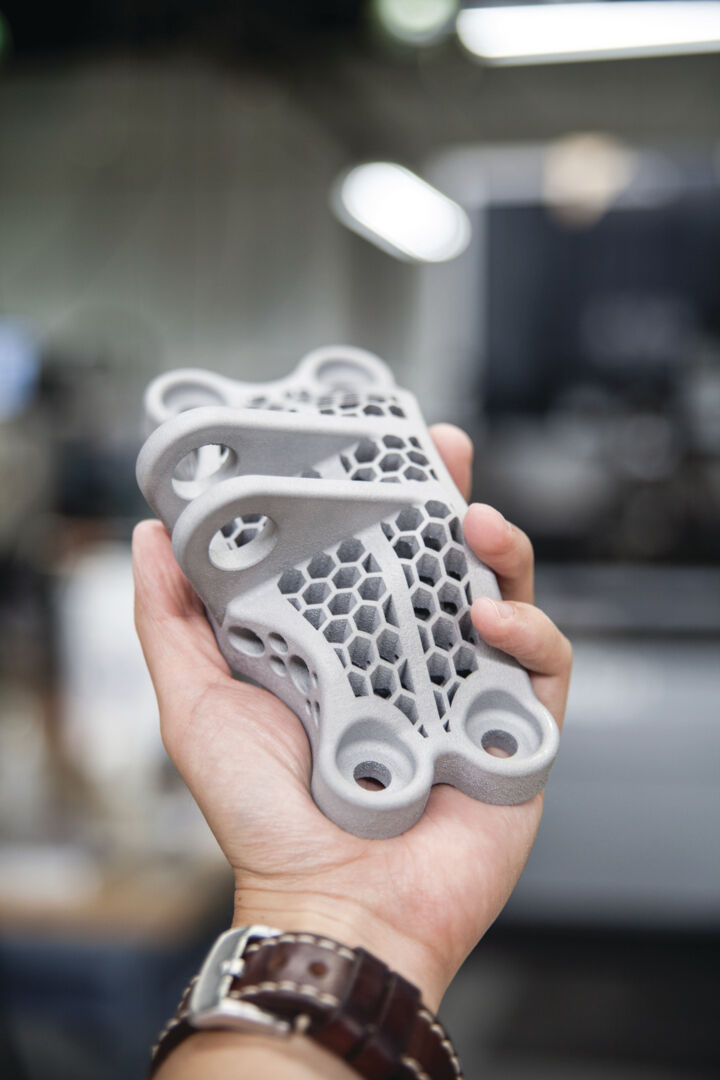
Metal 3D printing as shown here offers great potential for lightweight product designs.
Beware the Upload
“There are a lot of digital players out there, so many novices will upload their file to multiple sites and choose whoever has the lowest price or best delivery. But what’s crucial is to find one who will take the time to understand your requirements and not only help you to optimize your product, but the manufacturing process used to make it. For that, you need significant levels of engineering expertise,” Kahlon says.
DFM and its 3D-printing counterpart, design-for-additive manufacturability (DfAM), mean much more than managing part complexity. Kahlon ticked off a list of considerations: What level of process control do you need? How many critical dimensions do you have and what’s the sampling basis? Do you need to go through the production part approval process, or PPAP? What’s the plan for scaling to production? Are there potential compliance issues? How about long-term sustainability and carbon footprint considerations? These are just a few of the questions that should be addressed during the design stage. Each will impact part cost and viability but can’t be determined by simply uploading a file for an instant quote.
“We helped the consumer goods manufacturer Gel Blaster recently on a toy similar to a paintball gun,” Kahlon says. “They already had a design using injection molding, but needed a couple dozen quick yet durable prototypes for an upcoming trade show. After reviewing their design, we added several tabs to improve the assembly process, enlarged a number of fillets to make them more stable, and added some post-processing steps to elevate product appearance without impacting performance.”
There’s also San Francisco-startup Bimotal, which needed to create a compact, robust housing for a high-performance bicycle motor. To ensure the enclosures would be both durable and water-resistant, Stratasys Direct prototyped the components using a variety of materials, printing processes and post-processing techniques, ultimately opting for SLS printing using Nylon 12 GF for its mechanical properties. There were also some design changes, including adding 25% larger fillets for increased stiffness.
In a final instance of collaborative design, Kahlon’s team worked with Vivaquant on its RX-1 mini, a patch-style remote cardiac monitor. “We did a lot of early prototyping using stereolithography and PolyJet but knew the customer was always going to move to injection molding, in part because of the higher volumes, but also because the material they wanted was not available with AM. So we got our injection molding team involved and provided the customer with DFM feedback to avoid any redesign later on.”
None of these success stories would have been possible if customers had just uploaded their design and gone for the cheapest price, according to Kahlon. “The product development process is complex, so engage with your service provider and don’t be afraid to ask for help.”