
Like its big brother the hull-scale tool, the Jointless Hull subsection tool shown here can machine parts in the same handling, albeit much smaller ones.
It was around this time last year that we spoke with Nanci Hardwick, CEO of Meld Manufacturing Corp., Christiansburg, Va., who described her company’s metal additive manufacturing (AM) technology as both mesmerizing and “almost magical.” She was most excited about two recent developments—the introduction of 3PO, her latest Star Wars-inspired 3D printer, and the Army’s purchase of two custom Ingersoll Machine Tools hybrid systems that incorporate MELD Additive Friction Stir Deposition (AFSD) technology, one of which has earned the title “world’s largest hybrid metal 3D printer.”
Given the AM industry’s rapid pace of change, Hardwick’s tenure on the “world’s largest” throne will surely be short-lived. Sorry about that, Nancy. In the meantime, though, her colleague Dr. Matt Kelly isn’t concerned with temporary titles and claims of biggest, fastest, or most capable. He’s more interested in putting the AFSD technology to good use.
“The smaller of the two machines, called the Jointless Hull subsection tool, has a build envelope of roughly one cubic meter,” Kelly says. “It’s located at SAE International’s Advanced Manufacturing Commercialization Center (AMCC) in Sterling Heights, Mich. The Jointless Hull hull-scale tool is located at the U.S. Army’s Rock Island Arsenal in Illinois and has a build envelope of 30 x 20 x 12 feet (9 x 6 x 3.7 meters). Like the subsection tool, the hull-scale tool is a hybrid printer with five-axis machining capabilities, however its size makes it a very unique machine and capability.”
Meet the Magic
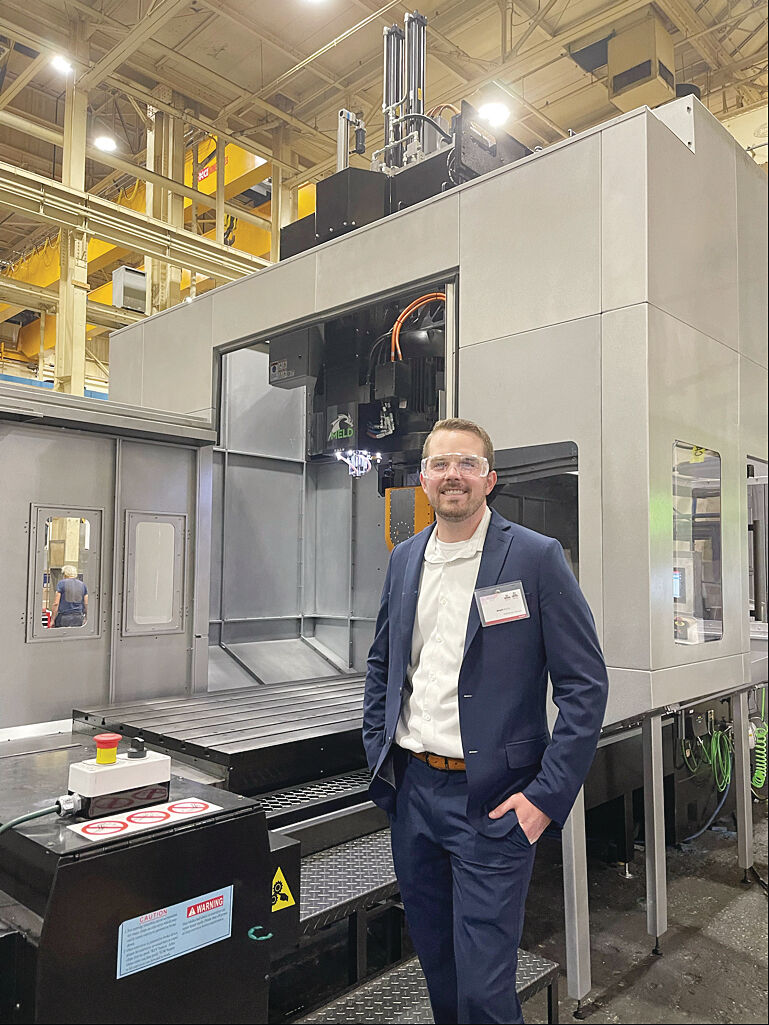
Matt Kelly, SME AM EP Chair—AM Technical Community Leadership Committee, Additive Manufacturing Technologist, Booz Allen Hamilton
Kelly, an additive manufacturing technologist at Virginia-based professional services firm Booz Allen Hamilton, is currently on contract with the U.S. Army DEVCOM Ground Vehicle Systems Center (GVSC) in Warren, Mich. He is the Army’s project lead for the Jointless Hull Project, a Department of Defense-funded effort in partnership with the Applied Science and Technology Research Organization (ASTRO) of America that aims to make armored combat safer and play a role in addressing supply chain vulnerabilities for castings, forgings and weldments.
It’s not surprising that Kelly was chosen for this project. While working on his doctorate at the University of Notre Dame, he spent extensive time researching linear friction welding (LFW) with induction pre-heating (a means to reduce the forces needed to complete a weld), which Kelly suggests would make the process easier and less expensive, thereby expanding its use.
LFW shares several commonalities with friction-stir additive manufacturing (FSAM) and AFSD, the latter used by MELD Manufacturing Corp., Christiansburg, Va. “Some folks like to compare it to directed-energy deposition, or DED, while others might try to categorize it as material extrusion, which is generally limited to polymers,” Kelly says. “But the fact is, AFSD doesn’t fit cleanly into any of the seven families of additive as defined under the ASTM F42 standards.”
Kelly notes that Hardwick commercialized the AFSD process less than six years ago, so there’s no reason for anyone to criticize the F42 committee quite yet. That being said, the group is well-advised to take a hard look at this emerging technology. “Right now we’re printing with 24-inch long, half-inch (610 x 12.7 mm) square bars of 6xxx and 7xxx series aluminum alloys at rates between 10-25 pounds (4.5-11.3 kg) per hour, but soon I can see us expanding into titanium and eventually steels,” says Kelly.
Do Me a Solid
AFSD is a solid-state process. Unlike DED and other fusion-based processes, there’s no phase change due to the metal transitioning from solid to liquid and back to solid again. Common solidification defects like porosity and hot cracking are therefore avoided.
“I’m not suggesting there aren’t challenges with additive friction stir deposition—as with any manufacturing process, additive or otherwise, it has its own unique set of pros and cons,” Kelly says. “But it’s our job as an industry to work through them and constantly improve.”
Despite the ongoing mission to develop armored vehicle hulls free of weld joints and other potential weaknesses, Kelly and his team continue to do just that. They’re not alone. U.S. Army GVSC is partnered with ASTRO America and a team of subcontractors to continue work under the Jointless Hull project.
Kelly also points to “the rich amount of work” being done at various universities, many of them MELD machine owners. “They’re printing different metals, evaluating the properties, and publishing journal articles on what they find. Academically, at least, it’s a very active space that is growing at a rapid pace. And even though industry hasn’t quite caught on, AFSD has some significant advantages over other AM technologies.”
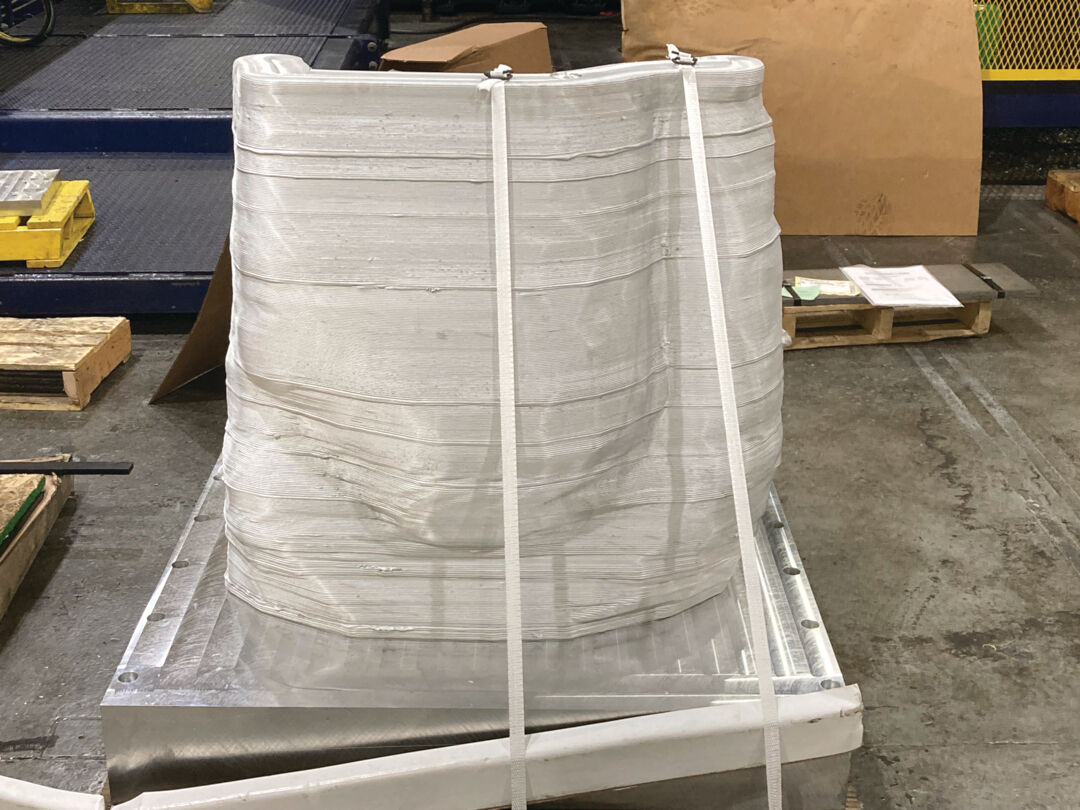
A hatch prototype for an Army vehicle 3D-printed using MELD Additive Friction Stir Deposition (AFSD) technology.
When not exploring AFSD’s potential, Kelly works with researchers at Auburn University (Ala.) and its National Center for Advanced Manufacturing Excellence (NCAME) on his other defense-related project—developing a defect-based approach for qualification of parts from the laser-powder-bed-fusion (L-PBF) process. It’s here that he gives a special shout-out to Nima Shamsaei, PhD, and Shuai Shao, PhD, both members of the school’s Samuel Ginn College of Engineering. The pair are “focused on the structure of 3D-printed materials and how that can be a predictor for performance rather than relying solely on mechanical properties,” Kelly notes.
How It’s Made
When asked how and when he became interested in 3D printing, Kelly’s answer was one that many television buffs can appreciate. “I grew up watching How It’s Made,” he laughs. “It was fascinating seeing how all these different everyday items are produced. Granted, I’ve always liked math and science, but that show is what got me passionate about manufacturing from a young age, so when I entered college, I found my way into the mechanical engineering school at the University of Notre Dame.”
It wasn’t until his senior year, however, that the word “additive” became part of Kelly’s scholastic pursuit when he took a class called Engineering Analysis of Manufacturing Processes. It was taught by the professor who would eventually become his post-graduate advisor, Steve Schmid, PhD, who gave students a reading assignment before every class and then “pulled names out of a hat” to ask questions about what they’d learned.
“The textbook we used walked through the basic engineering principles of every manufacturing process, and, as it turned out, preparing for those questions reinvigorated my love of the industry,” Kelly confides. “On exams, it was common for Schmid to draw a simple shape and have us list ten ways to manufacture it—3D printing was usually the catch-all. Simple questions like this were incredibly valuable, and brought back all those memories of watching How It’s Made. I began to realize that I wanted to make a career out of it.”
Entering A&D
That career began when Kelly accepted a position at Raytheon (now RTX Corp.), where over the next five years he would work on a range of activities, including several topology optimization and generative design projects that served to further his interest in 3D printing and the design freedom it provides. He also performed L-PBF simulations in an attempt to compensate for the distortion that often occurs, was a design engineer of test vehicles for cruise missiles, did structural analyses for underbody, jet-mounted radar-jamming pods and served as principal investigator on the America Makes project Additive for eXtreme Improvement in Optical Mounts (AXIOM).
Indeed, additive played such an integral role in these projects that Kelly used his experiences to help develop the internal website and training for RTX’s corporate Additive Manufacturing Center of Excellence. “Part of that involved putting together a design guide for internal use,” he says. “This gave me the opportunity to study AM further while helping other engineers learn the principles of designing for additive manufacturing.”
Speaking Out
Kelly is doing similar AM-centric work at Booz Allen Hamilton, where he recently celebrated his two-year anniversary. He’s also engaged in numerous speaking engagements. The most recent example was a presentation at the International Conference on Advanced Manufacturing in Washington, D.C., sponsored by the ASTM Additive Manufacturing Center of Excellence. He has also been active in the SME, serving as co-chair of the Technical Community Committee (TCC) with Jeff DeGrange of Impossible Objects for a time, and more recently serving as the chair of emerging professionals in AM within the AM Technical Community Leadership Committee.
Last October, Kelly participated in an SME-sponsored AM Summit near Detroit, where he and other industry experts shared insights and fielded questions. He saw many familiar faces, he says, representing “an impressive amount of knowledge and experience” from the medical, aerospace, automotive and other manufacturing sectors who discussed barriers for widespread adoption of AM. “The high rate at which AM technologies evolve, coupled with requirements for certification and qualification, make AM difficult to adopt in production,” he says. “That being said, there is an ongoing push to reduce costs without sacrificing quality and find ways to increase throughput.”
Kelly also believes that education and training can improve. “We as an industry must continue to educate students and emerging professionals on not only AM, but all manufacturing processes, so that designers are making the most out of what AM and other manufacturing processes have to offer.”